Cady Stribling
Features Editor
cstribling1@murraystate.edu
It’s heartwarming to witness Murray State members reinforcing Racer Pride and helping the community during a time of need. During the COVID-19 pandemic, assistant professor Rudy Ottway used technology to assist medical professionals.
Ottway created face shield apparatuses, visors that cover and prolong the use of surgical face masks in partnership with Kent Campbell, who works for local software company TapLogic.
“The Institute of Engineering became involved in 3D printing the visor frame when Keith Travis, vice president of institutional development at Murray-Calloway County Hospital, contacted Dr. Danny Claiborne, the department chair of the Institute of Engineering,” Ottway said.
Claiborne asked Ottway if he could support the needs of the hospital and reached out to junior engineering graphics and design major Clay Doron for assistance with the project.
They have worked tirelessly to supply 300 visors to the hospital and are now working to provide visors to Primary Care, Fast Pace and the Kentucky State Police.
Doron said by 3D printing the visor frames, they can make them for the hospital at a significantly lower price.
“The idea behind the face shield is that it can be worn over a traditional mask and prolong the life of those traditional masks,” Doron said. “The face shields can be sanitized and reused.”
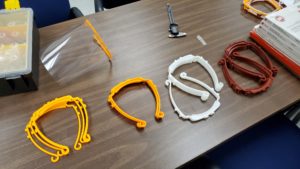
Doron said they are contacting other medical professionals around the area who are in need of them.
3D printing creates a physical object from a three-dimensional digital model. Ottway used a design from Sweden, which was shared worldwide so people can 3D print the visor frame.
There is another way to create the visor frames by creating a mold, however the visor frame is larger than what the molding equipment is able to produce.
The apparatuses help provide more facial coverage for medical professionals. The shield on the visor extends from the forehead to protect eye exposure and goes down past the chin.
“A 3D printer works by adding successive layers of material until the final part has been created,” Ottway said. “The process that we’re using to 3D print the visor frame is called material extrusion or fused filament fabrication.”
Ottway said the 3D printed visor frame is then paired with a clear transparency film to make a visor.
Creating the visors with 3D printing is quick, inexpensive and easily accessible. The Institute of Engineering owns several 3D printers that Ottway and Doron have been using.
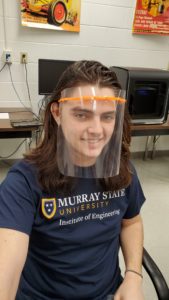
“We can 3D print a visor frame in about 45 minutes at a cost of less than $1 in material,” Ottway said.
Doron has used 3D printing in his classes, but the experience with this project taught him more than the classroom ever could.
Ottway and Doron have been working out of the Rapid Prototyping Center in the Collins Industry and Technology Center. While Doron works, he also balances school work.
“Each mask takes about 30 minutes to print, so while they are printing I can work on my school work,” Doron said. “The biggest thing is staying ahead of everything, staying organized and not waiting until the day before something is due to work on it.”
Doron said his parents are Murray State graduates and he’s lived in Murray his entire life, so helping to create the visors for medical professionals is important to him.
“Being able to help keep our local hospital staff safe and healthy during this crisis was its own reward,” Doron said.
Ottway said people across the campus and in the community have reached out to donate transparencies and their own 3D printers to help them.
“We are happy to help and are thankful that we’ve been blessed with resources to help in this time of need,” Ottway said. “The team effort from Murray State University has been phenomenal, and we appreciate all the support.”